Cost of Quality (COQ) System: How It Can Save Your Business Money
- Allan Ung
- Apr 21, 2023
- 6 min read
Updated: Mar 20
Allan Ung

“Eliminating what is not wanted or needed is profitable in itself.”
Philip Crosby
Introduction
In today's competitive business environment, quality is essential to success. Customers demand and expect high-quality products and services, and companies that fail to deliver will quickly lose their competitive edge. The key to ensuring quality is through the establishment of a Cost of Quality (COQ) system.
COQ is a business measurement system that helps to identify and reduce the costs associated with ensuring product and service quality. By establishing a COQ system, companies can measure their performance on quality and set targets for improvement, leading to cost reduction, improved customer satisfaction, and increased sales.
In this blog, we will explore the benefits of setting up a COQ measurement system and the four steps involved in implementing it. We will also provide guidance on how to prepare for a COQ program to ensure its successful implementation and sustaining the system.
What is Cost of Quality (COQ)?
By definition, the Cost of Quality (COQ) is the total cost of ensuring product and service quality. Total COQ is the sum total of the Cost of Non-Conformance (CONC) and the Cost of Conformance (COC).

Cost of Quality Tree
COQ can be summed up by the Prevention, Appraisal and Failure model, or, as it is more commonly known, the PAF model. Both prevention and appraisal costs are also commonly known as COC—the cost of doing things right the first time. Internal and external failure costs are known as the CONC—the cost incurred as a result of things not being done right the first time.
Benefits of a COQ System
Establishing a Cost of Quality (COQ) system provides several benefits to an organization, including:
1. Cost reduction: By identifying and reducing the costs associated with poor quality, a COQ system can lead to cost savings for an organization.
2. Improved customer satisfaction: Ensuring product and service quality through a COQ system can improve customer satisfaction and loyalty.
3. Increased sales: Providing high-quality products and services can lead to increased sales and customer retention.
4. Competitive advantage: A COQ system can help an organization differentiate itself from its competitors by demonstrating a commitment to quality.
5. Better decision making: The data collected through a COQ system can provide valuable insights into an organization's performance and help in making informed decisions.
6. Process improvement: Analyzing COQ data can help identify areas for improvement in processes and systems, leading to increased efficiency and productivity.
7. Prevention of problems: By identifying and addressing quality issues before they occur, a COQ system can prevent costly problems from arising in the first place.
Overall, a COQ system can help organizations achieve a culture of continuous improvement and excellence, leading to increased profitability and long-term success.
Preparing for a COQ Program
Before establishing a COQ program, it is important to prepare and plan for its implementation. Here are some key steps to follow in preparing for a COQ program:
1. Form a COQ Committee: The first step in preparing for a COQ program is to form a committee that will oversee the program. This committee should include representatives from all relevant departments and functions within the organization, including quality, production, sales, and finance.
2. Appoint a COQ Sponsor: In addition to forming a committee, it is important to appoint a COQ sponsor. This person should be a senior executive within the organization who has the authority to provide the necessary resources and support for the COQ program.
3. Identify a COQ Program Manager: The next step is to identify a program manager who will be responsible for overseeing the day-to-day operations of the COQ program. This person should have experience in quality management and should be able to work closely with the COQ committee and sponsor.
4. Define Scope of COQ Program: Before implementing the COQ program, it is important to define its scope. This includes identifying the products, services, or processes that will be covered by the program, as well as the specific quality costs that will be measured and tracked.
5. Provide COQ Education and Training: To ensure that all employees understand the importance of the COQ program and are able to participate effectively, it is important to provide education and training on COQ concepts, methods, and tools. This can be done through workshops, seminars, and other training sessions.
6. Commit Necessary Resources: Finally, it is important to commit the necessary resources to support the COQ program. This includes funding for training and education, as well as the resources needed to collect, analyze, and report COQ data. It is important to ensure that everyone in the organization understands the importance of the COQ program and is committed to its success.
The Four Steps of a COQ System

The Four Steps of a COQ System
Step 1: Identify COQ Items
The first step in implementing a COQ system is to identify quality cost items that contribute to COQ. This step focuses initially on the Cost of Non-Conformance (CONC) items. The organization can develop a COQ checklist and evaluate the identified COQ items to determine if they can be calculated and reduced or eliminated. The organization can also source available COQ data and match accounts with COQ to determine the precise amount of cost associated with each item.
Step 2: Collect & Report COQ Data
The second step is to collect COQ data and provide a monthly status report to the COQ committee for information and evaluation. The organization can calculate or cost the COQ items using various methods, such as Whole Account, Unit Pricing, Whole Person, and/or Labor/Resource Claiming. The organization can also develop forms to allow for the input of all information for the identified COQ items and provide a monthly status report to the COQ committee.
Step 3: Analyze COQ Data
The third step is to analyze the data carefully and thoroughly and identify opportunities for improvement. The organization can analyze the COQ data and prioritize the COQ items for improvement using trend analysis when past and present data is available and variance analysis when there are goals or targets set for performance. The organization can also set targets for improvement based on the analysis.
Step 4: Improve Quality and Reduce COQ
The final step is to improve quality and reduce the COQ of the prioritized items. The organization can assign process owners or quality improvement teams to address the prioritized COQ items and communicate COQ performance by using various methods such as COQ scorecard, meetings, newsletters, emails, etc. The organization can also make improvements using systematic methods such as the PDCA cycle and the "QC" tools, standardize the corrective actions, expand the COQ program to include the Cost of Conformance (COC) items, and institute a prevention system through continuous improvement of processes, products, and services.
Sustaining a COQ System
Sustaining a Cost of Quality (COQ) system is a continuous process that requires a long-term commitment from an organization. To sustain a COQ system, it is essential to constantly understand and meet the needs of customers, as their satisfaction is directly linked to the success of the program. Additionally, COQ should be viewed primarily as a cost reduction program and must be managed as such. Senior management support across multiple functions is critical to the success of COQ, and a holistic approach that positions COQ as part of a Total Quality Management (TQM) program can lead to optimum results. It is also important to focus on prevention rather than a quick fix, and to provide rewards and recognition to motivate employees to participate in the program. To ensure continuous improvement, it is crucial to evaluate and improve the COQ system periodically, keeping in mind that Total Quality is a journey rather than a destination.
Conclusion
In conclusion, the COQ system is a vital tool for organizations that are committed to improving product and service quality. It is a measurement system that allows organizations to identify the cost associated with ensuring quality and provides a framework for reducing those costs. The four steps of a COQ system, which are identifying COQ items, collecting and reporting COQ data, analyzing COQ data, and reducing COQ, provide a structured approach to improving quality and reducing costs. However, preparing for a COQ program by forming a committee, appointing a sponsor and program manager, defining the program's scope, providing education and training, and committing necessary resources is equally important. Sustaining a Cost of Quality (COQ) system is a continuous process that requires a long-term commitment from an organization. By implementing a COQ system, organizations can achieve significant cost savings, improved customer satisfaction, and increased sales.
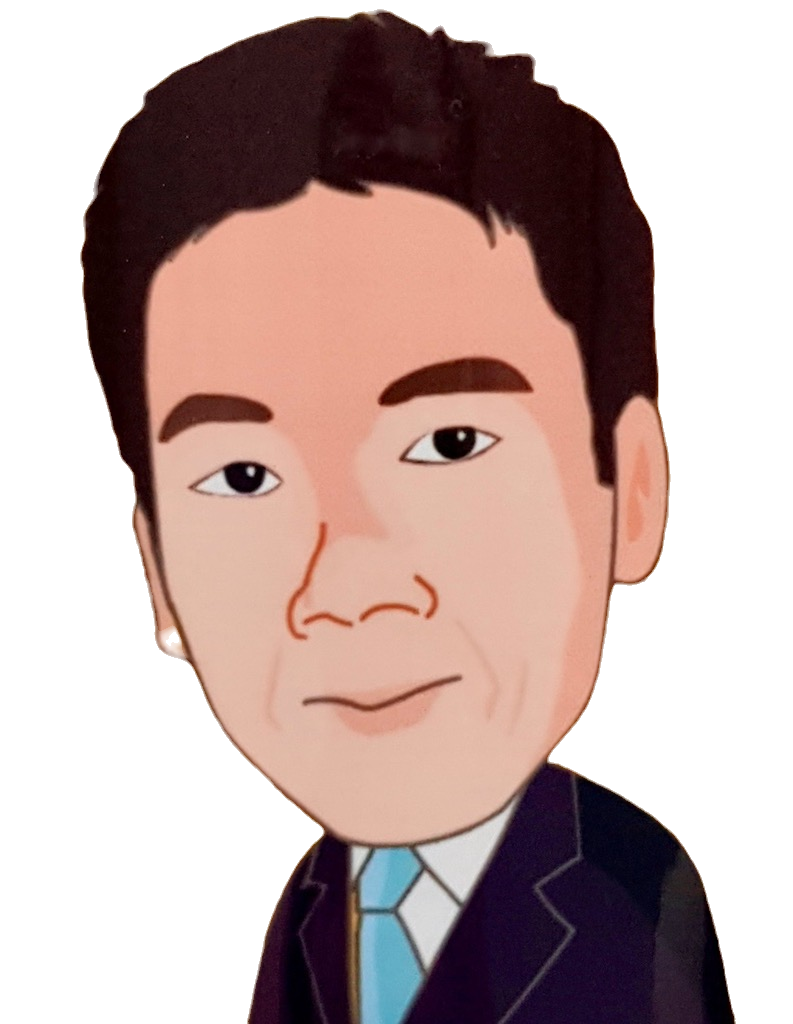
Article by Allan Ung, Principal Consultant at Operational Excellence Consulting, a distinguished management consultancy based in Singapore. Our firm specializes in maximizing customer value and minimizing waste through the strategic adoption of Design Thinking and Lean management practices. For further details, please visit www.oeconsulting.com.sg
Comentarios