
value stream mapping workshop
Visualize Processes. Eliminate Waste. Create Flow.
Description
Value Stream Mapping (VSM) is a powerful Lean management tool that enables organizations to visualize and understand the flow of materials and information through their value streams. By mapping current processes from end to end, VSM helps teams identify bottlenecks, delays, inefficiencies, and non-value-adding activities — the hidden waste that erodes customer value and business performance.
This hands-on, practitioner-oriented training equips participants with the skills and tools to map current states, envision future states, and develop practical action plans for improvement. The course integrates Lean thinking, Kaizen principles, and structured VSM methodology to guide participants in transforming operations for flow, speed, and customer-centric value delivery. Participants will gain practical experience through real-world case studies, group exercises, and a step-by-step roadmap for facilitating VSM workshops within their organizations.
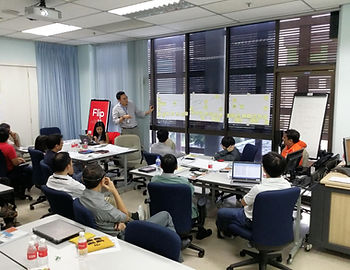

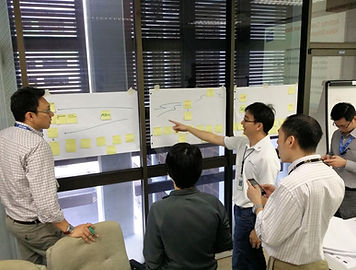
Recommended Audience
This training is ideal for Lean practitioners, improvement leaders, operations managers, engineers, and cross-functional team members involved in process transformation and waste elimination initiatives.
Methodology
This course is interactive and hands-on, featuring:
-
Expert-led presentations and real-world case examples
-
Group exercises and mapping simulations
-
Step-by-step guidance on VSM application
-
Practical tools, worksheets, and templates for immediate use
Learning Objectives
By the end of the course, participants will be able to:
-
Understand the principles and objectives of Value Stream Mapping within the Lean framework.
-
Apply the VSM methodology to visualize current-state processes and identify various forms of waste.
-
Develop future-state value stream maps that enable improved flow, reduced lead time, and enhanced customer value.
-
Facilitate and contribute to VSM workshops effectively within cross-functional teams.
-
Use VSM outputs to drive actionable improvement plans and Kaizen initiatives.
Workshop Outline
Module 1: Introduction to Value Stream Thinking
-
What is a Value Stream?
-
Purpose and Business Benefits of VSM
-
VSM in the Lean Management System
-
Value vs. Waste: The 8 Types of Waste
-
Role of VSM in Continuous Improvement
Module 2: Current-State Mapping Methodology
-
Identifying the Product or Service Family
-
Defining Customer Requirements and Takt Time
-
Mapping the Process Flow, Material Flow, and Information Flow
-
Data Gathering Techniques (e.g., Gemba walks, observations)
-
Calculating Key Metrics: Lead Time, Cycle Time, Inventory, and VA/NVA Time
Module 3: Analyzing the Current State
-
Interpreting VSM Symbols and Flow Data
-
Identifying Bottlenecks, Delays, and Waste
-
Root Cause Exploration Using Flow Gaps
-
Discussion of Real Case Examples
Module 4: Designing the Future State
-
Future-State Mapping Principles (Flow, Pull, Takt, and Load Leveling)
-
Implementing Supermarkets, FIFO, and Heijunka
-
Determining the Pacemaker Process
-
Building a Future-State Vision and Target Condition
-
Lean Flow Enablers and Standard Work Considerations
Module 5: Creating an Implementation Roadmap
-
Developing a VSM-Based Action Plan
-
Prioritizing Improvement Opportunities
-
Linking VSM to Kaizen, PDCA, and Daily Management
-
Change Management and Stakeholder Engagement
-
Sustaining Gains Through Visual Management and Metrics
Module 6: Facilitating Effective VSM Workshops
-
Roles and Responsibilities in a VSM Team
-
Facilitator Tips and Best Practices
-
Workshop Tools, Templates, and Logistics
-
Overcoming Common Challenges and Pitfalls
Award of Certificate
Certificate of Attendance will be issued to participants who have attended at least 75% of the workshop
Duration
One-day and two-day programs are available